"Red
Iron" is a nickname for Pre-Engineered Steel Buildings.
This style of construction uses big solid web I-Beams to span the
width. These are commercial buildings and are best suited for 50' to
120' wide.
Red Iron Buildings are what is called a "pinned design" in
engineering-speak. That means that it requires big concrete piers in
the ground to pin it from spreading.
A Red Iron Building usually costs more per square foot to build;
however, they hold their value well. Typically, Red Iron Buildings
are less expensive per square foot the bigger they get. They are the
building of choice for Airplane Hangers, Crane Buildings, Riding
Arena's, large Strip Malls, multistory, or anything that is just
big.
Red Iron Buildings are typically insulated with 3" thick PSK faced
fiberglass roll insulation. The 3" gives a pre installed R-10 value.
Most business owners in Arkansas would refer to this as a well
insulated building. You have the option to do more. We offer the PSK
backed fiberglass roll insulation in 4" thick that gives a pre
installed R-13 value and 6" with a pre installed R-19 value.
.jpg)
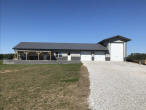  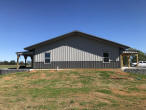 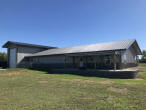
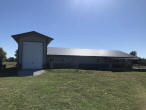 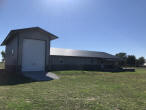 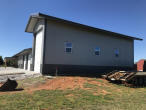 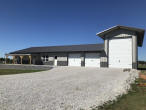
Typical construction letter and why you need one.
Just
about any wind load or snow load desired can be had in a Red Iron
Building. One characteristic trait of a Red Iron Building is that
they are more complicated to finish out the interior.
Red Iron Buildings can have a dirt floor, like for a riding arena.
We will install large concrete piers in the ground for the main
frames. The pier sizes will be determined by the buildings
horizontal reactions. This piers-only design is often used for
big-roof-only buildings used for equipment storage.
Piers and Footer is another option. The piers hold the building in
place and the footer seals up the building. It is possible to heat
and cool a building that still has a dirt floor.
Piers, Footer and Concrete Floor is the more traditional route for a
commercial building.
If pulling a 80,000 pound semi into your building is in your future,
we can build your floor to handle it. Our typical severe duty
concrete floor consists of having a 4" rock base finely graded; a 6
mil thick poly vapor barrier; #3 Rebar held in proper position with
chairs; on a 2' x 2' grid pattern, 3,500 pound concrete mix at least
6" thick. Control joints cut in while the concrete is still green;
keeping the sections less than 400 square feet each. This formula is
heavy duty and screams "bring it on".
Steel Building experience
I, Scott Yarbrough, am so old that when I first got into
pre-engineered buildings we used books, not computers to price them.
Back then every manufacturer had their own take on how to engineer a
steel building. Each manufacturer had their own size of purlins,
their own panel profiles, their own haunch connections, etc. If you
wanted to add onto an existing building, and wanted it to match
perfectly, you had to go back to the original manufacture and pay
through the nose. They had you.
During the mid 90's the invention of Metal Building Software created
an industry standard. I was hesitant of MBS at first, because I had
already learned seven different in-house software programs. However,
being one of the very first people to learn MBS, at one of the very
first companies that gave them a shot, has turned out to be
invaluable to me. That same industry standard still holds true
today. This allows me to add onto almost any existing building and
not beholden to any one manufacturer.
By knowing the MBS program like the back of my hand allows me to
create distinctive looking buildings, while still being economical.
These steel buildings can be manipulated like an old girlfriend, or
boyfriend, whatever the case may be. By just moving standard
economical parts around, a person can create a "T" shaped building
with differing eave heights; an octagon or something amazing without
having to go through the added expense of an Architect (not that
there is anything wrong with hiring an Architect).
There is a lot more to getting the customer exactly what they want,
at an economical price, than just shooting off a quote request to
another state and seeing whatever comes back.
|